
Texas Space Grant Consortium
The Texas Space Grant Consortium is a group of 65 institutions which include universities, industrial organizations, non-profit organizations, and government agencies within Texas that are joined to ensure that the benefits of space research and technology are available to all Texans. In a broader context, the National Space Grant Program, consisting of 52 Space Grant Consortia nationwide, cooperate to achieve this goal for all Americans.
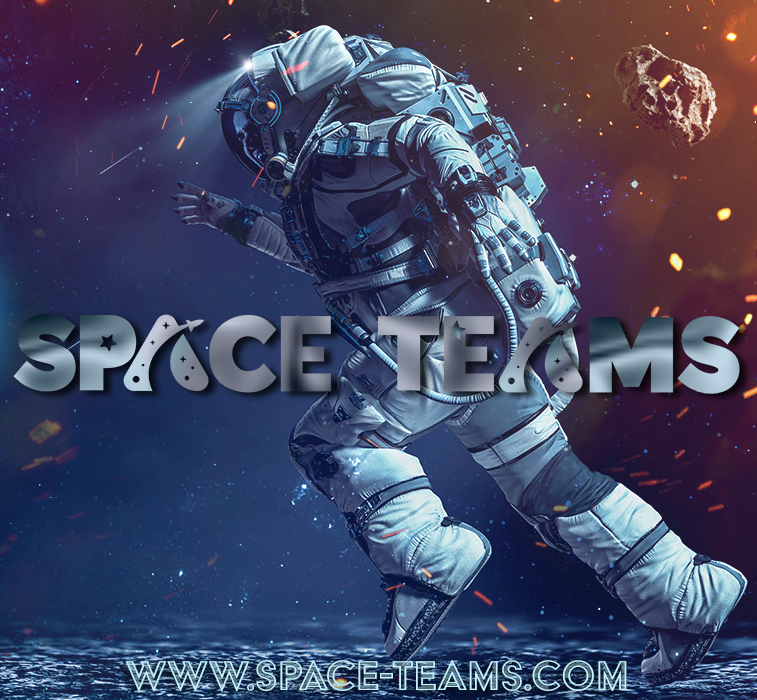
Space Teams
Middle- and high-school students, design your own interplanetary space missions! Educators, visit Space Teams Lab to learn about getting NASA-sponsorship. Attention undergraduate and graduate students: join the Space Teams University: Mars City Design Competition, launching March, 2024! Everyone, join the 6-day Global Space Challenge. Next mission launches 2024!
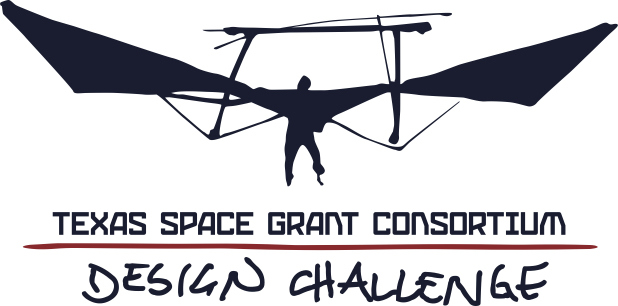
Design Challenge
Applications for the Spring 2024 Texas Space Grant Consortium Design Challenge have now closed. Learn more about the Spring 2024 Teams here or check out last year’s contest on our YouTube channel.
For more information contact Tim Urban.
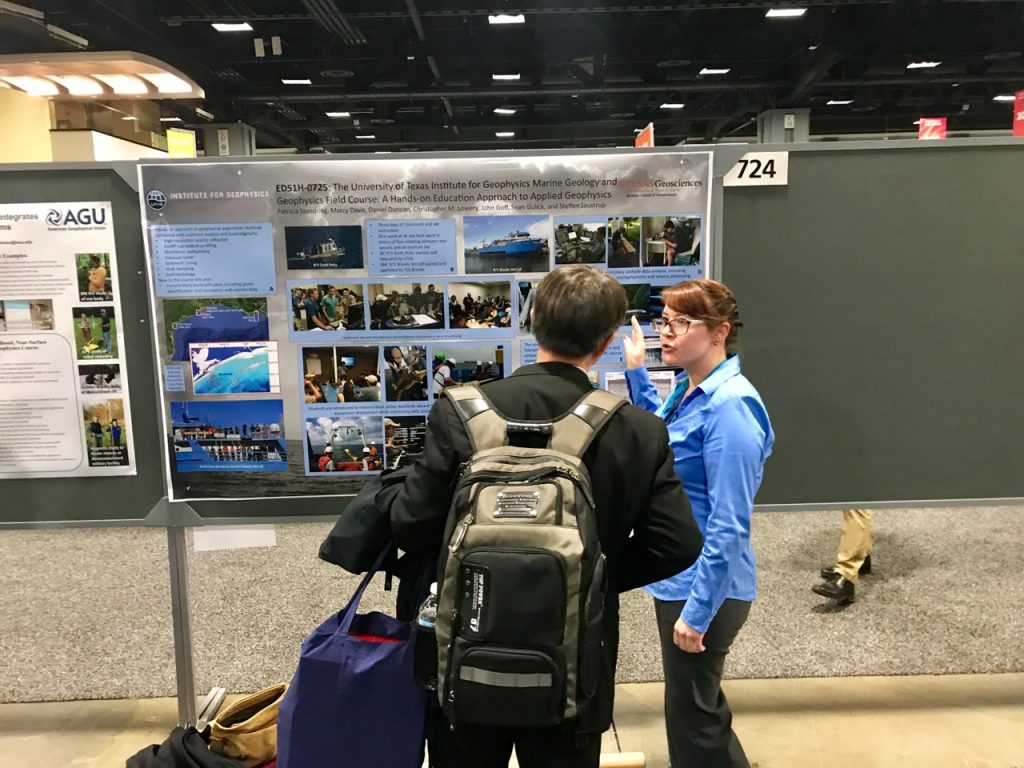
Fellowships and Scholarships
Graduate and undergraduate students at Texas Space Grant academic institutions are eligible to apply for a Texas Space Grant scholarship or fellowship. Learn more.
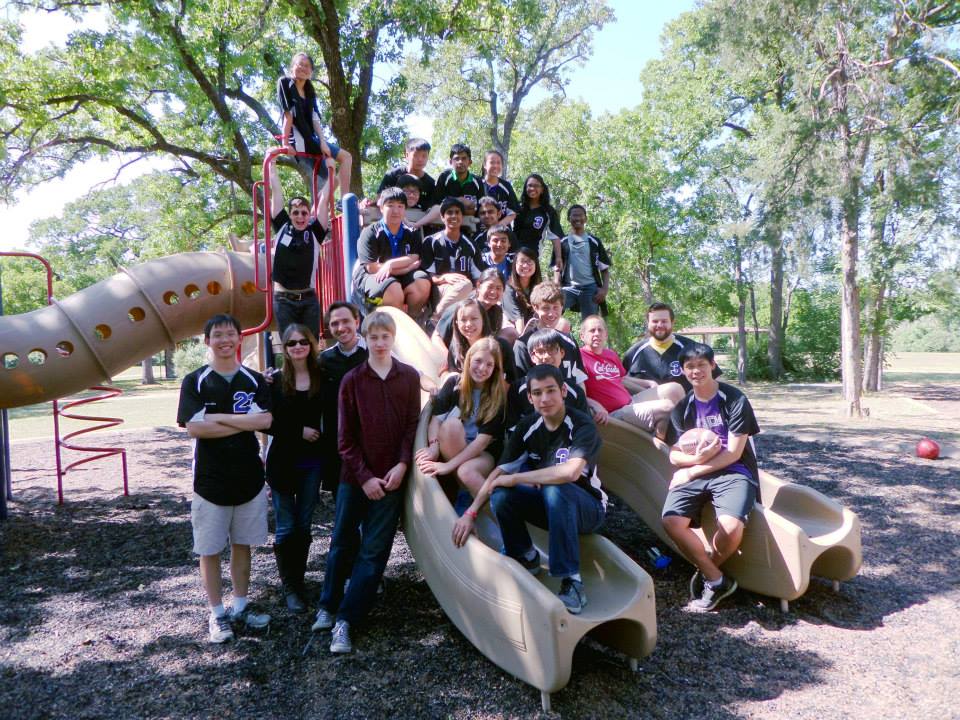
K-12 Education
Texas Space Grant supports K-12 programs that get students excited about math and science through space based activities. Supported programs include Space Teams Labs, Camp SOAR, SSEP and the LiftOff Summer Institute. Learn more.
Contact
Learn about our Board of Directors.
Dr. Tim Urban, Director
urban@tsgc.utexas.edu
Talia Jurgens, Program Manager
jurgens@tsgc.utexas.edu
Phone: 512-471-3583
Design Challenge: designchallenge@tsgc.utexas.edu
Space Teams Labs: spaceteamslabs@tsgc.utexas.edu
Scholarships: scholarships@tsgc.utexas.edu
Fellowships: fellowships@tsgc.utexas.edu
Located at the University of Texas Institute for Geophysics
Texas Space Grant Consortium
10100 Burnet Road
Austin, TX 78758
University Mail Code R2200